From CAD to 3D: Automating Design Files for Machinery
When it comes to engineering and machinery design, Computer-Aided Design (CAD) has significantly transformed the industry. It improves workflows, offering practical benefits that extend beyond mere efficiency. It enables users to visualize the assembly of complex machine parts, such as gears, and verify the functionality of their designs before the construction of physical prototypes. This tool streamlines production processes and minimizes errors, ultimately enhancing productivity in manufacturing. Consequently, it has opened new possibilities for business growth, such as the use of immersive technologies.
By harnessing the potential of 3D models generated from CAD files, companies can explore various applications, from showcasing complex machinery to providing interactive training for personnel. This article delves into the automation of converting CAD files into 3D models and highlights the existing limitations. It also presents tsukat strategic solutions for addressing these specific challenges in the machinery industry. By exploring these hurdles, you’ll gain valuable insights that can drive enhanced efficiency and innovation in operations.
Challenges in Automating CAD Files for 3D Visualization
The introduction of Computer-Aided Design (CAD) has revolutionized the industrial and machinery sectors. It offers numerous benefits, including enhanced machining capabilities, greater design detail, and improved collaboration. Additionally, it has led to significant time and cost savings, establishing CAD as an efficient tool for businesses. As technology evolves, companies seek further productivity gains through automation, including automating the processing of CAD files for 3D interaction.
To fully leverage the benefits of CAD, we first need to convert CAD designs into 3D models suitable for visualization, and a process called tessellation is crucial here. Tessellation breaks down the complex curves and surfaces of the CAD data into a series of simpler shapes, such as triangles (polygons). This transformation allows for easier rendering and visualization in 3D, and efficient processing on various devices. After tessellation, optimizing the model is essential. This step involves techniques like polygon reduction algorithms and Level of Detail (LOD) adjustments. Thanks to tessellation and model optimization, the model’s efficiency is ensured across different platforms and applications.
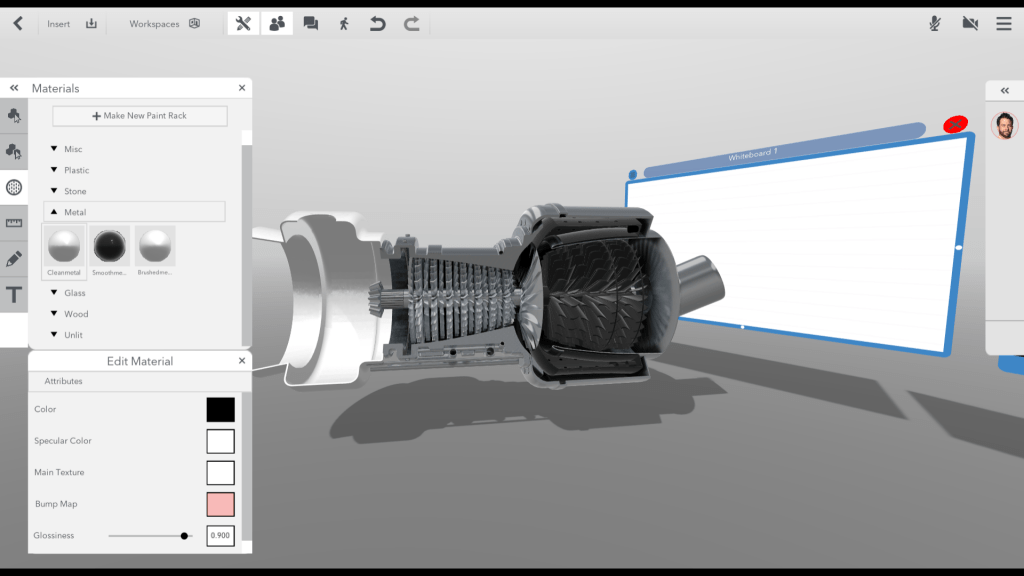
Yet, achieving full automation in this domain remains challenging due to several factors.
The first aspect is the trade-off between performance and accessibility. Original CAD format files are large and require high-end devices to work with effectively. Using high-fidelity solutions that capture every detail produce visually impressive 3D models, but require costly supercomputers and specialized software, limiting accessibility and feasibility. On the other hand, solutions designed for real-time visualization on readily available devices like laptops and tablets may compromise on detail and visual quality. Such offset can lead to less accurate representations of machinery and potentially confusing end users.
Another significant challenge is the need for manual intervention. Despite advances in automation, human expertise is still crucial for making informed decisions during conversion. For example, a technical expert might simplify details for a 3D model meant for basic training, while a more detailed model is necessary for complex manufacturing simulations.
Solutions for Efficient 3D Visualization
As it becomes clear, achieving perfect automation in integrating Computer-Aided Design (CAD) files across different devices is challenging. However, there are practical solutions: model optimization and content streaming. These approaches balance visual fidelity, functionality, and user interaction, enhancing CAD file usability across various platforms.
Model optimization demands a combination of partial automation and manual adjustments, such as polygon conversion, texture and shader application, and interactivity setup. This method offers advantages like mobility, enhanced user engagement, and maintained visual quality. Users can manipulate the model, zoom, and rotate it while prioritizing both visual detail and efficient file size. This approach is ideal for web and local applications where a balance between aesthetics and efficient delivery is crucial.
However, the complexity of the original CAD data significantly impacts the effort required for optimization. This dependency relies not only on the quality of the CAD data but also on the algorithms used for the conversion process. It’s worth noting that optimizing complex models may result in a slight decrease in their visual quality. With such intricate designs, metadata becomes crucial. It includes all the essential details about a model, such as its specifications and version history. This information is necessary for making accurate updates and modifications. It also allows for easy tracking of changes over time and helps maintain the model’s integrity, especially when multiple revisions are involved.
Model optimization offers a versatile approach thanks to its flexibility and compatibility with robust local systems. This feature enables the creation of intricate visual representations and simulations for various operational scenarios. Applications can range web previews for quick evaluations to comprehensive project reviews on PCs.
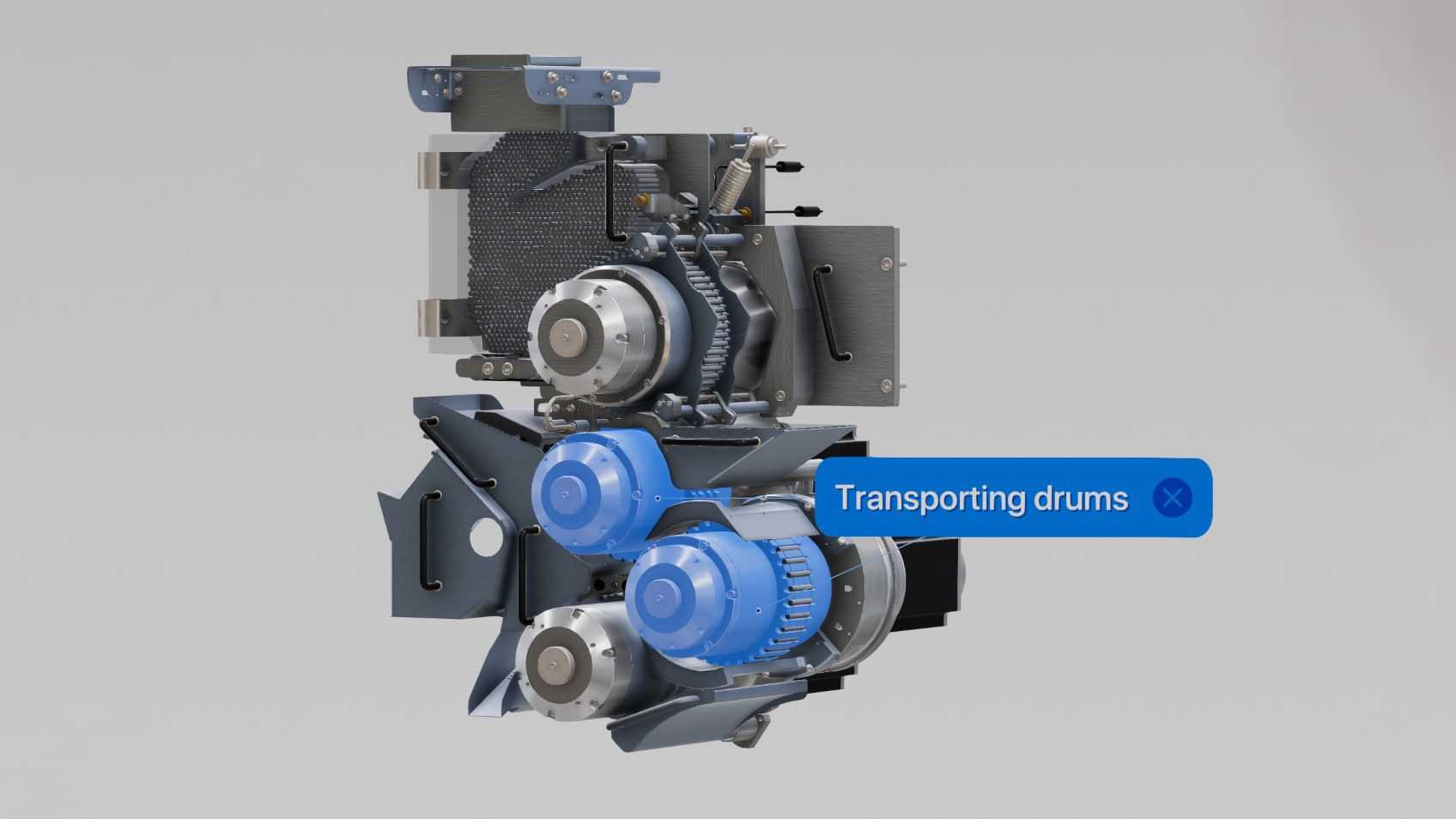
Alternatively, content streaming, such as Pixel Streaming technology from Epic Games, offers a different approach. It runs an application and its environment on a dedicated cloud workstation capable of handling CAD files or high-quality auto-converted models. The system then streams the output directly to the user’s device, enabling mobile accessibility, interactive options, and high-end visual quality. This technique is particularly well-suited for mobile and VR devices. The automatic conversion and updating of CAD files are performed on a remote server, ensuring secure and fast processing.
Content streaming also offers more scalability. Cloud resources provide a substantial advantage for collaborative design projects and real-time visualization needs. These systems can handle multiple users simultaneously, making it easy for them to access complex CAD models.
Yet, it does come with some drawbacks, primarily the cost of cloud computing resources can be high. Additionally, a consistent internet connection is crucial. Without it, there could be lag during streaming, impacting the overall experience.
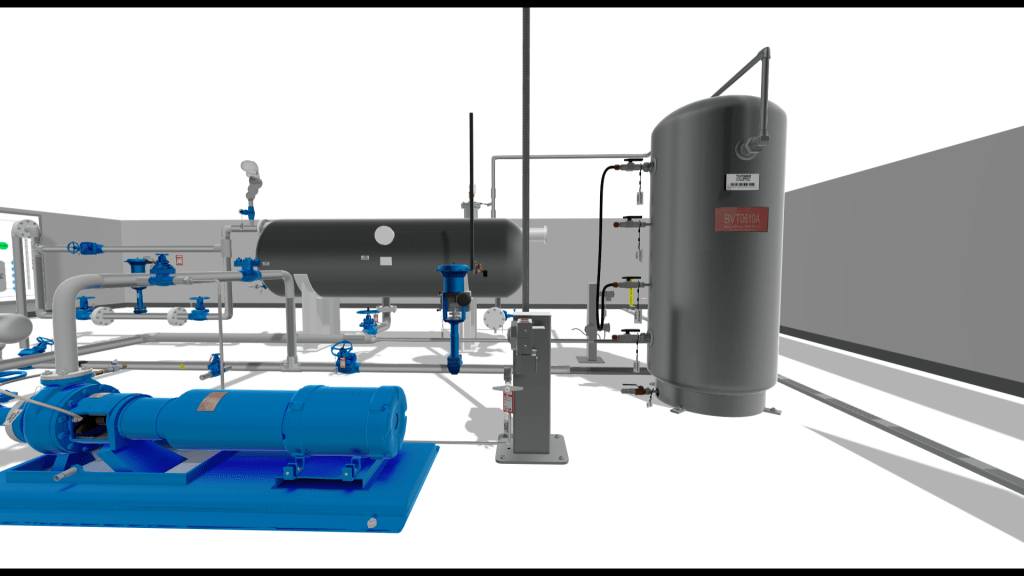
Custom Optimization and Update Solution
Updating CAD files for 3D visualization requires a robust process. Recognizing this need, we have focused on developing tsukat’s custom automated system for updating CAD elements in 3D models, allowing clients to efficiently replace any part within a model. This capability ensures both accuracy in the updated model and a smooth workflow. A significant benefit is that it does not require rebuilding the 3D scene.
- Software-Driven Model Preparation
CAD files are created in the NURB (non-uniform rational B-spline) format, which is well-suited for modeling complex and detailed curvatures. During export, these files can be converted into a triangular mesh format to facilitate compatibility across different platforms. For successful processing, the file must be in the NURB (solid) format, contain proper metadata, and follow clear naming conventions. The next step involves using software to incorporate this new element into the 3D visualization model.File Processing Settings:- Level of Detail (LOD) Adjustments one of the first steps in replacing the model. It prioritizes which parts of the model should receive high-fidelity representation. Higher LOD captures more details but demands more processing power, while lower LOD minimizes performance impact but might obscure smaller components.
- Visibility Settings: Determining visibility settings is crucial for optimizing computational resources and prioritizing critical aspects. For example, if a client needs to view a PC mouse in a model, it is better to hide the mouse’s internal components. This selective visibility ensures that the model remains streamlined and efficient, focusing on the exterior design while reducing unnecessary processing load by omitting less pertinent details.
- UV Mapping enhances the model’s realism by unwrapping a 3D model onto a 2D plane, which facilitates the accurate projection of textures onto the model.
- Version Control and Automatic Updates
Our solution leverages version control to continuously monitor and automatically apply the latest updates to the assembly process. This feature eliminates manual update requests by instantly recognizing changes made to the CAD specifications of individual components. Once detected, these changes automatically update the corresponding 3D models, ensuring they are always up-to-date. - Automated Optimization and Intelligent Data Management
Upon completion of the initial processing, the software automatically optimizes the updated CAD file using predefined settings tailored to your machine’s capabilities. Additionally, our system conducts detailed metadata analysis, extracting essential information such as unique ID codes, model descriptions, and connectors for different parts. This data supports intelligent searches within our database, ensuring precise matching and updates to the correct models. - Model Update and Integration Process
At the end of the optimization process, our system executes an automated update sequence, replacing the older file version with the latest version in the database. This process ensures that all project instances using this file are immediately updated. Our system also guarantees that the model’s current functionalities and features remain intact while incorporating updates. The updates are smoothly integrated into the new model and optimized to avoid any unforeseen changes in its behavior.
As a result, the client receives the final updated model with all the requested enhancements and optimizations. This automated workflow minimizes human error and significantly speeds up production cycles.
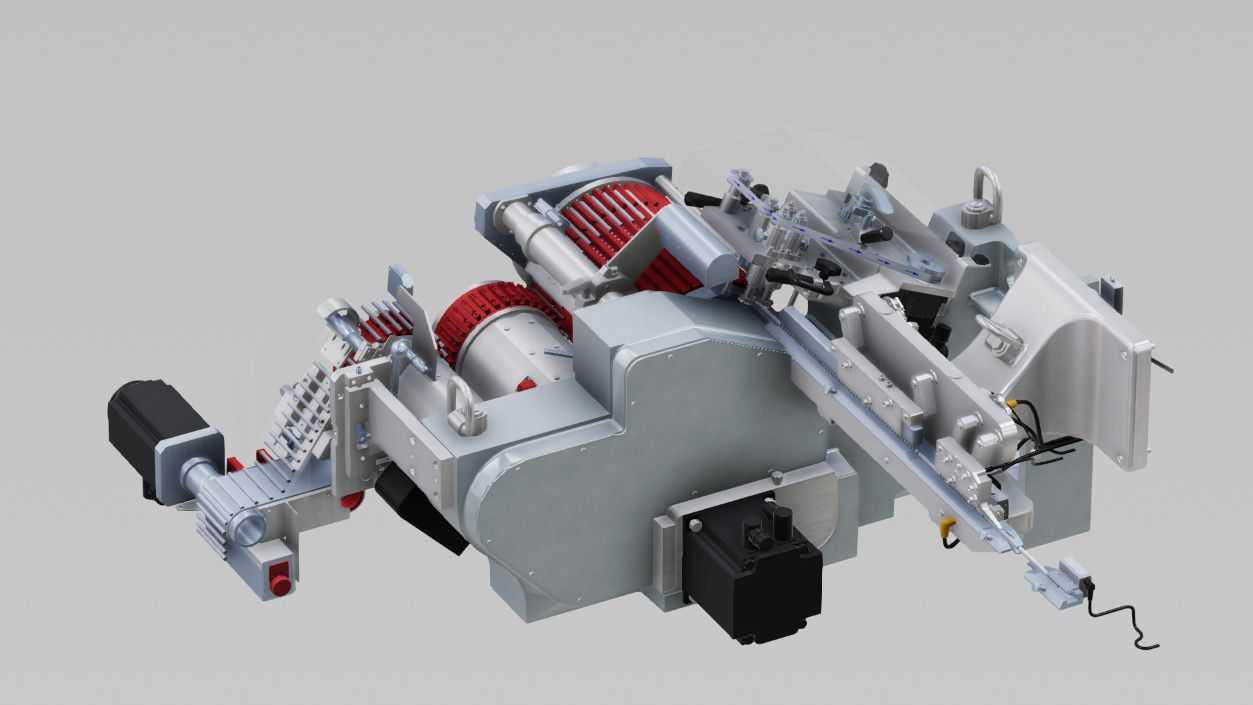
Conclusion
Since 2017, tsukat’s skilled engineers have leveraged various approaches to optimize CAD files for immersive 3D presentations and interactive learning experiences. We understand the challenges inherent in CAD automation from both technical and business perspectives. Therefore, our custom-designed solutions are crafted to address these specific obstacles, enhancing the efficacy and impact of your projects. Visit our service page to learn more about how we can assist your cause.