Körber VR Robots
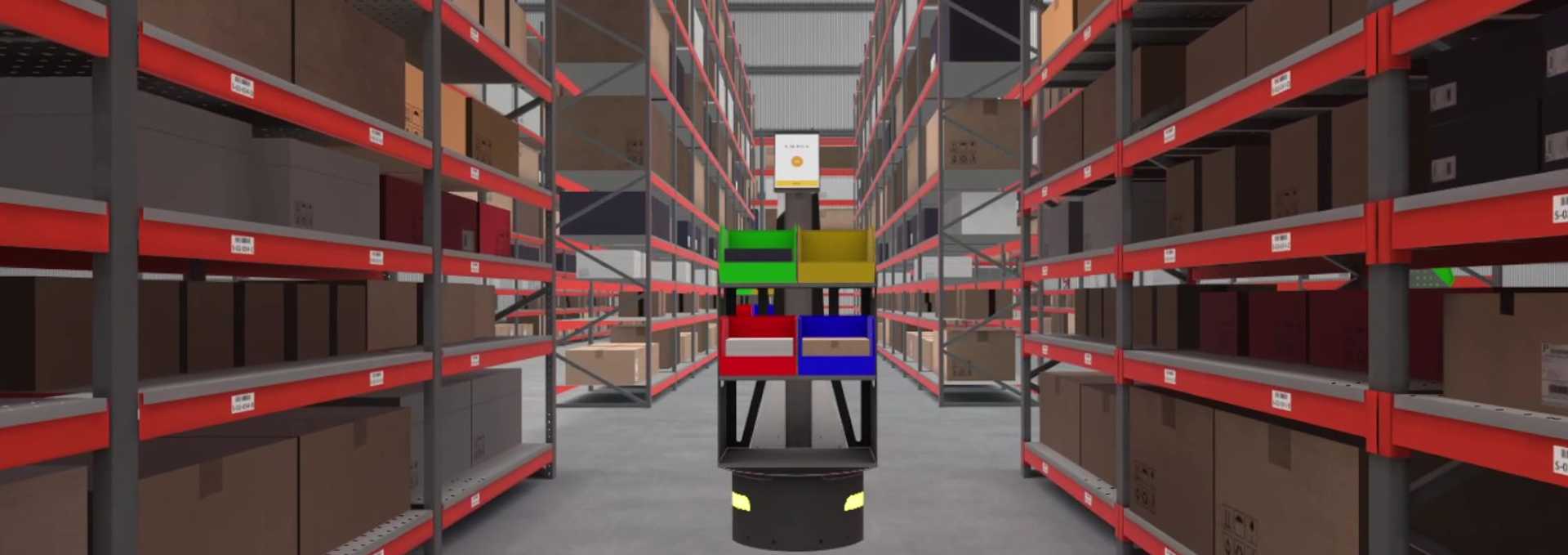
The Korber Robots project was created as a VR experience for warehouses’ logistics and operations with the help of the robotic system. The main gist of this case is to present people the opportunities for the automation of production or manufacturing processes with the help of robots. By interacting with robots through their performance, people can save time, effort and use robots as reliable assistants to perform their work as quickly, efficiently, and qualitatively as possible.
The VR experience allows us to work with two types of robots and each has its own function and workflow:
1. Goods To person. The process of working with this kind of robot is quite simple. The mobile robot consists of a computer monitor, a fixed scanner, a mounted handheld scanner, a step ladder on wheels, and put to light with a tote on each side of the pick module.
A mobile robot displays a shelved rack containing boxes of various sizes and colors to an opening. The process starts when the monitor’s screen shows the pick location (level and side), an image of the item to pick (a box of a specific size and color), and the required quantity. The picker will choose the indicated item and quantity asked by the robot, scan it with a fixed scanner, and check the monitor for the location of the tote on the put-to-light wall. The picker will then go to the put location, place the items in the tote, and press the put-to-light wall button to finish the pick.
Once the first pick is complete, the picker will return to the pick port, where a new bot positions itself for the next pick. The picker will repeat the same process for the second pick.
2. Collaborative In Aisle Picking. In the aisle, multiple mobile robots with totes will be positioned at different locations, each representing a robot ready for picking. The picker will approach the closest robot and view the screen, which displays an image of the item to be picked, including its bin location and quantity.
After the picker selects the item and quantity, they will scan it on the robot and confirm the quantity. The robot will then indicate where the item should be placed on the robot. The robot has four put locations, each represented by a different colored tote and labeled position 1-4 on the screen. The picker will put the item in the indicated tote and press the confirm button on the robot’s screen.
The robot will then proceed to the next pick. After completing the second pick with the first robot, the robot will move on, and the picker will approach the next closest robot to begin the process again for a single pick.
The client of the project has used this experience on several events and received overwhelmingly positive feedback that makes us be proud of our tsukat team.